In the current rapidly evolving manufacturing landscape, the quest for productivity, accuracy, and cost efficiency is crucial. As sectors strive to meet rising demands and reduced production times, the technique of injection molding has emerged as a leading technology that promises to revolutionize the way goods are created. This flexible process is more than molding materials; it represents a major change towards more green and innovative manufacturing practices.
Injection molding technology services provide a wide range of advantages that make them favorable to organizations of any size. From producing complex geometries with incredible accuracy to facilitating the use of a diverse range of materials, this technique stands out in its ability to streamline production while upholding high quality. As we delve deeper into the benefits of injection molding, it becomes apparent why this method is set to play a key role in the upcoming of manufacturing.
Advantages of Injection Molding
One key advantages of injection molding is its efficiency in producing high volumes of parts. This manufacturing process allows for quick production times, making it ideal for businesses seeking to scale up their operations. Once the mold is created, parts can be produced in a few seconds, significantly reducing the time from concept to market for new products. This efficiency not only enhances output but also reduces labor costs associated with manufacturing.
A further advantage of injection molding is the precision and consistency that offers. The process enables the creation of complex shapes and intricate designs with elevated tolerance levels. This level of detail is hard to achieve with other manufacturing methods. Moreover, the stability of the injection molding process means that part quality remains uniform batch after batch, which is crucial for maintaining brand reputation and meeting customer expectations.
Cost-effectiveness is also a key factor that makes injection molding a preferred choice among manufacturers. While the initial investment in mold creation can be high, the sustained savings in production costs make it economically viable for large-scale production. Materials used in injection molding are often more cost-effective than alternatives, and the ability to reuse scrap materials further enhances cost savings. Businesses choosing injection molding services can benefit from these reductions and still ensuring the quality and durability of their products.
Applications of Injection Forming in Multiple Industries
Injection molding is broadly used throughout various industries due to its versatility and productivity. One major application is in the vehicle sector. Companies utilize injection molding to create sophisticated parts such as instrument clusters, safety shields, and internal components. The technique allows for the production of thin yet resilient parts that meet rigorous safety and performance standards. The ability to produce high volumes of consistent quality components makes injectable molding essential for meeting the requirements of modern automotive production.
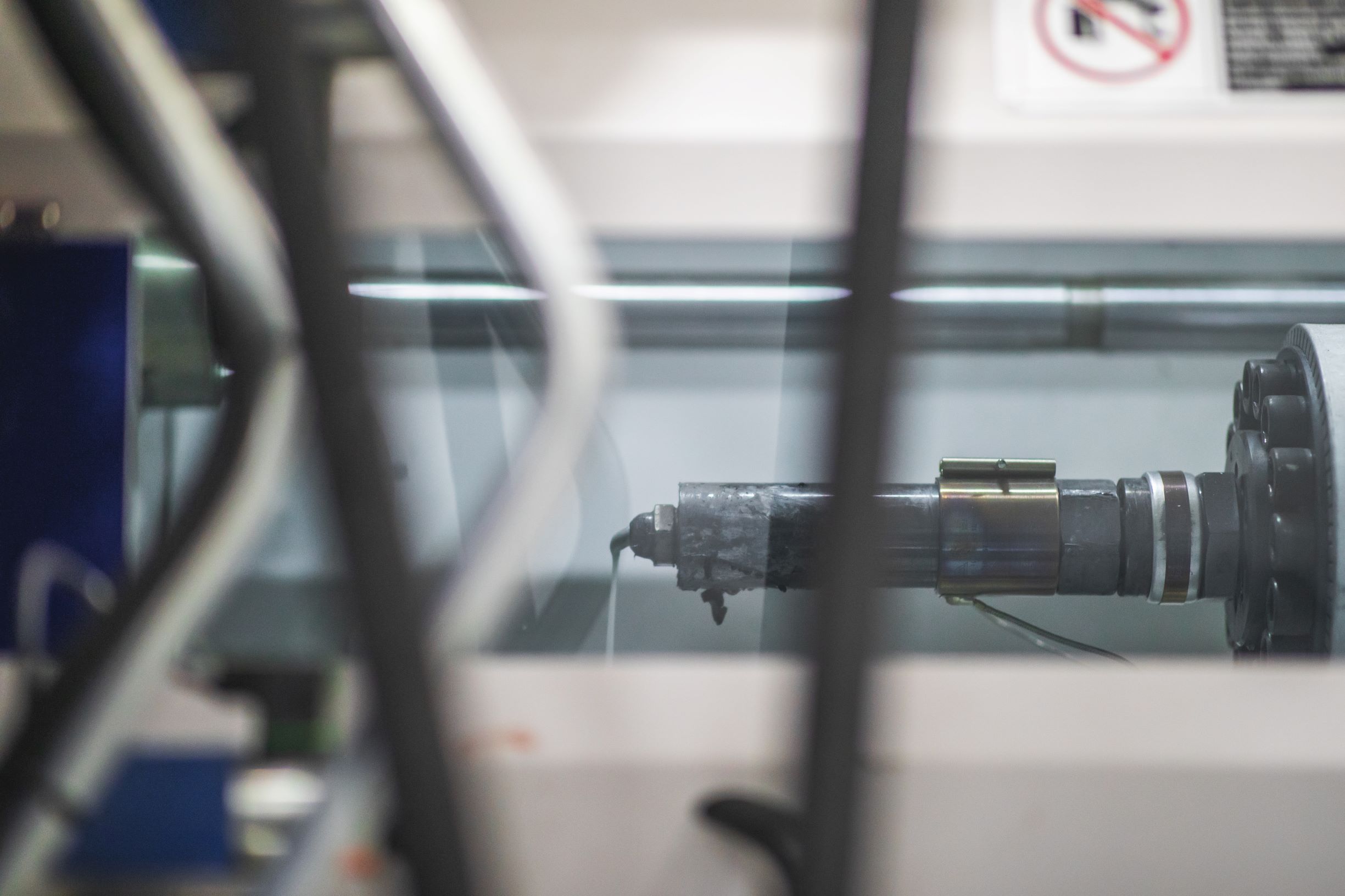
Another major industry that gains from injection forming is personal electronics. Devices such as cell phones, slates, and wearable devices rely on injection-formed parts for their enclosures, controls, and internal structures. The precise and detailed designs made possible through injectable molding allow for advanced product design while preserving a high level of appearance and utility. As tech continues to evolve, injection forming plays a crucial role in enabling rapid prototyping and bulk production of new electronic products.
In the healthcare field, injectable molding is essential for producing various tools and devices, including injections, operating tools, and housings for electrical medical equipment. The technique not only facilitates the production of precisely made, sanitary components but also assists the development of bespoke solutions for medical practitioners. With the growing demand for advanced medical devices, injection forming services are crucial for ensuring that products are produced to the top standards of excellence and regulatory compliance.
Emerging Advancements in Injection Molding Technology
As the requirement for precision and efficiency in manufacturing grows, injection molding technology continues to advance. One significant trend is the integration of advanced materials, including biodegradable and repurposed plastics, which address the growing focus on sustainability. Companies are investigating innovative materials that not only meet operational standards but also reduce ecological footprint. This shift towards more sustainable materials is likely to transform product design and manufacturing techniques in the immediate future.
Another significant development involves the adoption of automation and Industry 4.0 technologies in injection molding services. Smart factories equipped with IoT devices enable real-time oversight and data collection, improving productivity and minimizing idle times. Automated systems, such as robotic arms for part handling and quality control, streamline manufacturing processes and improve precision, allowing that manufacturers can deliver top-quality components at a quicker pace.
In conclusion, the growth of 3D additive manufacturing and 3D fabrication is impacting conventional injection molding methods. While injection molding continues to be the preferred method for large-scale manufacturing, the ability to rapidly create prototypes using 3D fabrication enables companies to develop designs and test concepts more swiftly. This combination of methods is paving the way for blended manufacturing strategies, where injection molding is utilized in conjunction with additive manufacturing to enhance flexibility and customization in product development.